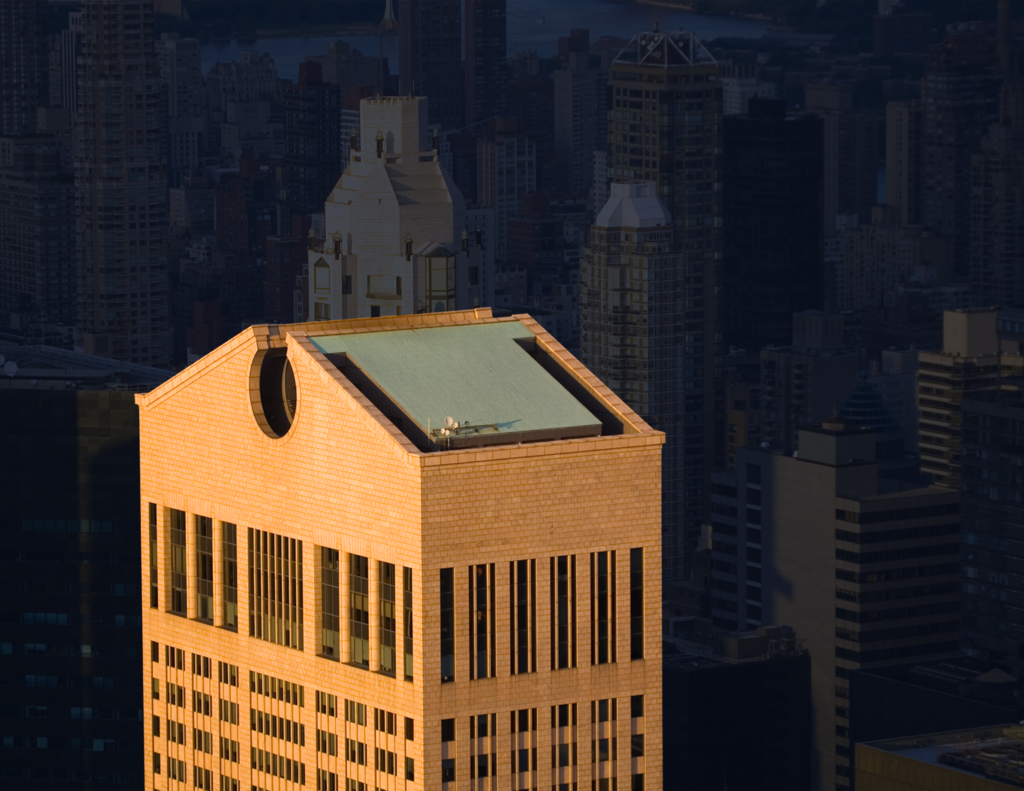
Known to many as the Sony Tower and before that as the AT&T Building, the famed landmark skyscraper standing at 550 Madison is one of the latest to see a major renovation.
THE EARLY CONTROVERSY OF 550 MADISON
Originally completed in 1984, the structure by Philip Johnson & John Burgee became a lightning rod as soon as it was announced in 1978 due to its Postmodern design, featuring a grand arch, stone facade and, most especially, its broken pediment roof widely thought to resemble Chippendale furniture. Following decades of dogmatic Modernism, with Johnson in a leading role, a new age in architecture had arrived and with it a new criteria for judging it: humor.
Paul Goldberger, American Architecture critic most notably known for his “Skyline” column in The New Yorker, wondered if the Chippendale part “suggests that a joke is being played” that in the end “may not be quite so funny.” Others dismissed the top as a “historicist joke” (art critic Robert Hughes) and a crass “one-liner” (architectural theorist Charles Moore).
To supporters, the joke was on the haters. “There is humor in his AT&T design,” architecture critic Paul Gapp agreed, hoping that in response American architecture “will stop boring us to death.” Johnson for his part did not deny his intentions. “Let’s have fun,” he said in an interview.
Architectural writer Susan Doubilet saw it as “a serious attempt to bring humor” to building design. That concerned architectural historian Frank Beckum. “If he’s doing it as a joke, then that’s alright… but if he’s doing that thing as a serious answer to the problem of today’s skyscrapers, it’s a tragedy.” Goldberger smiled in the end. When it was completed he called the Chippendale a “happy presence.”
THE RECENT CONTROVERSY OF 550 MADISON
The Manhattan landmark was acquired by Olayan Group in 2016. A year later, the developer announced a partnership with Snøhetta to revamp the skyscraper. But the design, which would have replaced much of the building’s facade with a glass wall, did not sit well with preservationists and architecture critics.
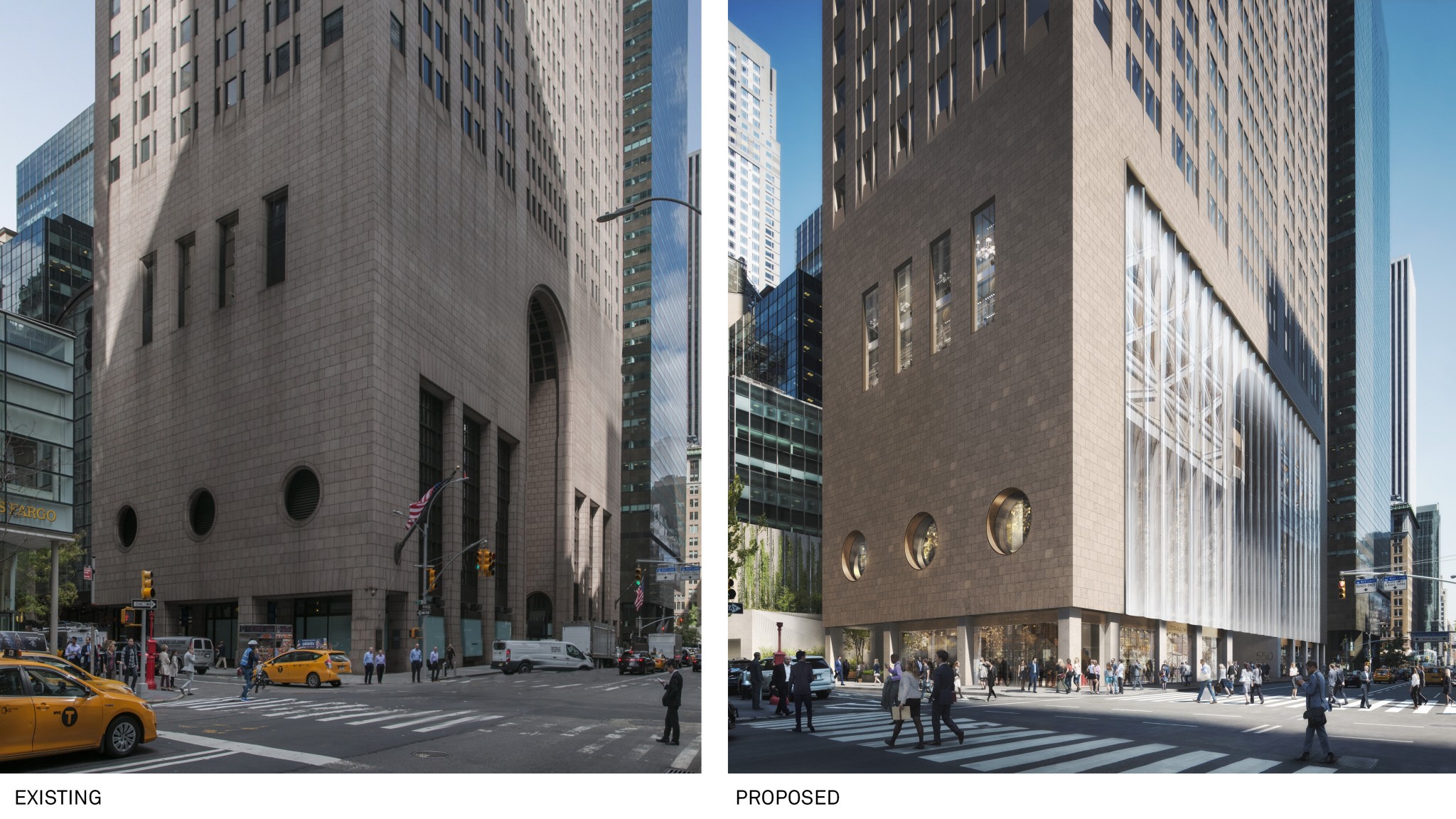
The original design concept by Snøhetta’s development team, which would have replaced much of the building’s facade with a glass wall, did not sit well with preservationists and architecture critics.
The development team went back to the drawing board, and in 2018, unveiled a new “preservation-first” design for the building’s exterior and POPS. To create that new space, builders will remove some of the existing retail and dismantle an annex that was added when Sony owned the building in the 1990s.
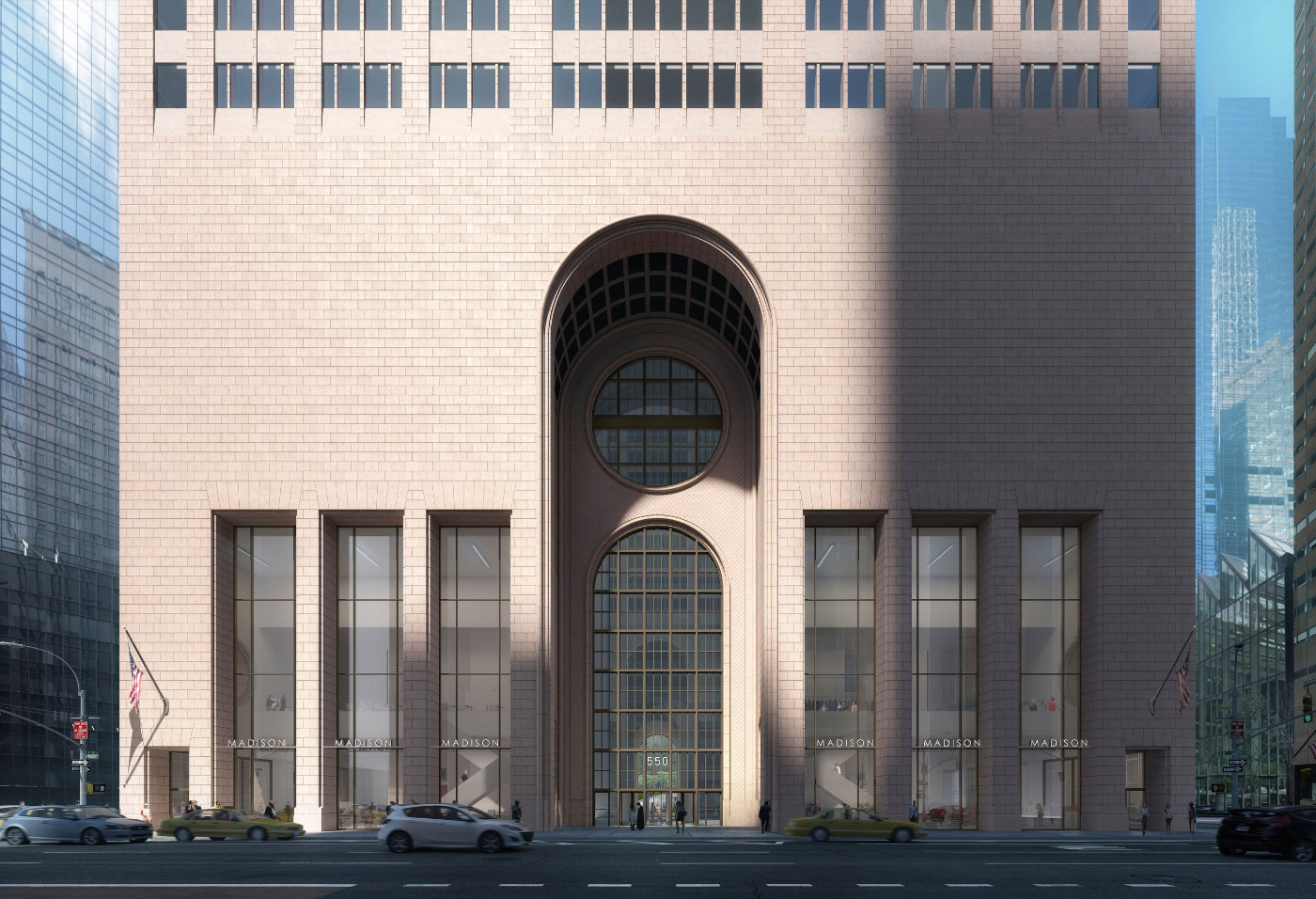
Redesigned “presentation-first” concept for the exterior base and POPS of 550 Madison Ave.
Currently, the 37-story building has 852,830 square feet of rentable mixed-use space. The building features approximately 776,000 square feet of office space, prime retail frontage on Madison Avenue, and exhibition and museum space.
At its base, the redesigned interior lobby features a LEED® Platinum and WELL Gold certified open public garden space designed by Snøhetta—a result that earned both public and industry praise in stark contrast to the backlash from their initial design.
The design firm plans to transform the dark, underutilized space (which is a Privately Owned Public Space, or POPS), into an airy garden with a glass canopy and plenty of greenery.
The garden links to the building’s lobby—also in the midst of a transformation—and will boost the site’s footprint by 21,000 square feet. Nearly half of that will be planted with an array of evergreens, perennials, and flowering shrubs to create a lush green space that offers a retreat from midtown’s glass and steel skyscrapers while celebrating the “Northeastern climate,” says Michelle Delk, head of landscape architecture at Snøhetta.
“This new garden complements the adjacent tower while drawing upon the vibrancy of the neighborhood and the natural history of the region, offering visitors an immersive respite in the city.”
– Michelle Delk, Head of Landscape Architecture at Snøhetta
But amidst all the drastic changes at its base, the now-iconic “Chippendale” pediment at the peak of 550 Madison, which has occupied a pivotal part of the Manhattan skyline for almost 40 years, remains. However, it has been given new life thanks to Barrett’s Black Pearl® Cold Applied Asphalt Protected Membrane Roof System. And with that, it will remain strong & protected for the next 40 years among the rest of the cloud piercers in the concrete jungle.
THE VERSATILITY OF BLACK PEARL® COLD APPLIED ASPHALT
Barrett’s Black Pearl® Waterproofing System is composed of two primary products:
• Black Pearl® Primer Adhesive
• Black Pearl® Sheet Membrane
These components are based upon the same core formula of select, unoxidized asphalt cement base, butyl rubber, styrene isoprene styrene (SIS), neoprene rubber, styrene-butadiene-styrene rubber (SBS), carbon black, fillers, plasticizers and curing agents. The Black Pearl Primer Adhesive also has an aliphatic solvent that is within acceptable OSHA and EPA current regulations.
Black Pearl® Sheet Membrane is a 55 mil woven polyester fabric providing extra tensile strength and stability. This fabric is impregnated and coated with the Black Pearl® rubberized formula. The compatibility between the two components is 100 percent, with the Black Pearl® Primer Adhesive acting as a catalyst on the sheets and chemically fusing the system elements together (including flashings) into a thick, semi-monolithic waterproof membrane.
Most Black Pearl® applications are over concrete substrates, exterior grade plywood, blindside lagging, sheet piling, cement board and even asphalt protection boards are also acceptable substrates with some waterproofing designs. Consultation and peer reviews are encouraged and welcomed.
Black Pearl® is an all-season material that can be installed anytime between 0°F and 100°F, eliminating stocking and out of date problems. Black Pearl® systems are compatible with extruded and expanded foam boards, PVC, EPDM, drain mats, asphaltic materials and coal tar pitch. It also has the unique ability to be applied to green and damp concrete.
BLACK PEARL® PROTECTED MEMBRANE SYSTEM
Proudly made in the USA, Barrett’s cold applied Black Pearl® asphaltic systems offer guaranteed protection for a number of different roofing & waterproofing applications. In this instance, the building utilized our Black Pearl® Protected Membrane Roofing System.
Installed by the exterior construction and contracting team at Related Services, LLC, the application was also inspected and approved by Joseph Strickland. Additionally, the completed installation passed its EFVM test administered by IR Analyzers.
Click through the gallery below to see images from the application process.
(Photos courtesy of Joseph Strickland)