HyppoCoat 100
HYBRID POLYUREA/POLYURETHANE GREEN CONCRETE WATERPROOFING MEMBRANE
-
TECHNOLOGY
Hybrid Polyurea/Polyurethane
-
MATERIAL
Modified Urethane
-
APPLICATION
Fluid Applied
-
INSTALLATION
Single Component
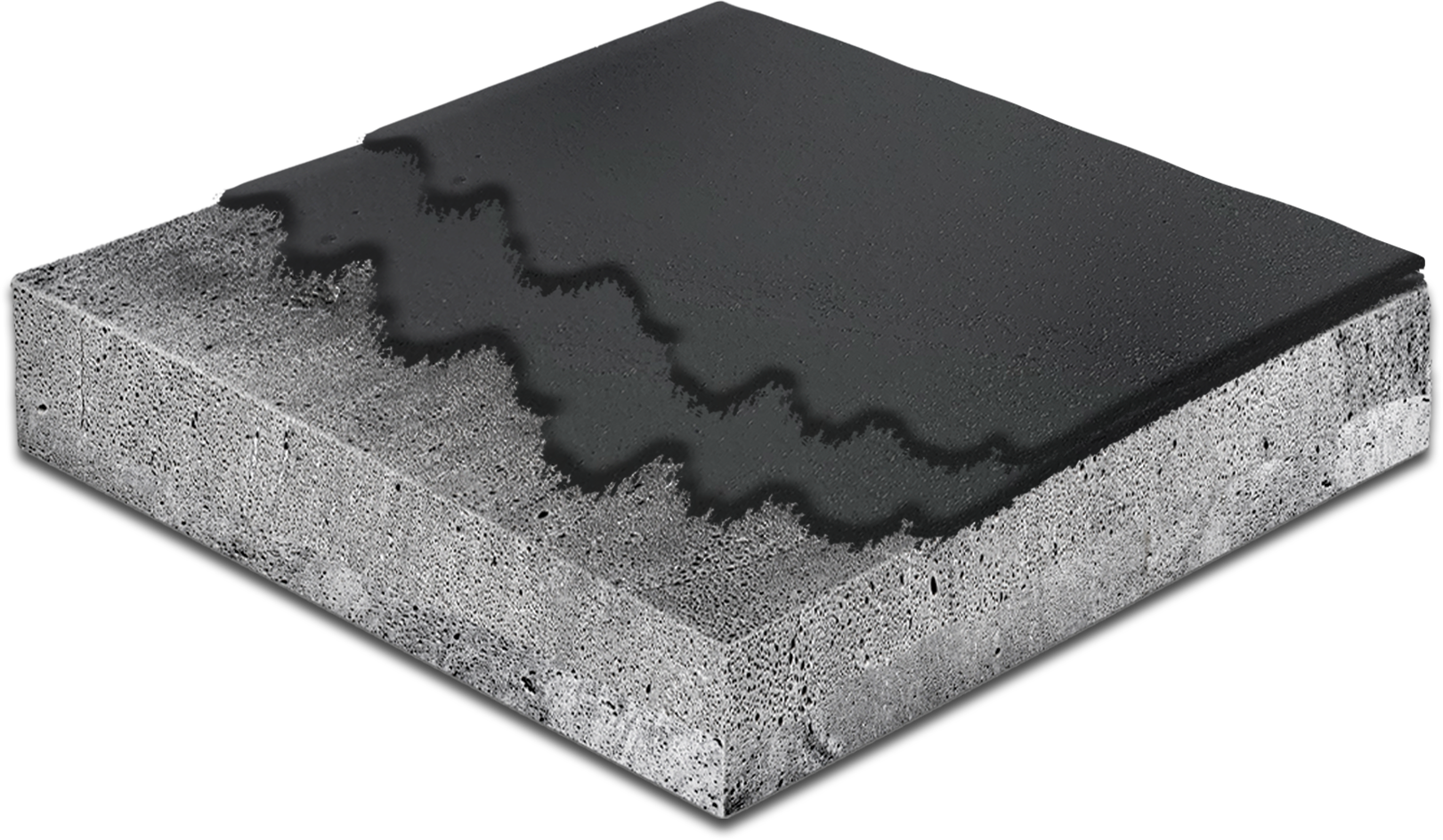
DESCRIPTION
HyppoCoat GC (Green Concrete) is a user-friendly, high solids, single component, liquid applied membrane for cured or green concrete. The system uses two coats of a modified urethane coating and protection board to create an elastomeric system designed to expand and contract with normal structural movements.
HyppoCoat GC is easy to use and can be applied immediately after green concrete forms have been removed, providing a quick return-to-service window during application. It also acts as an aggressive barrier against harsh chemicals, abrasive wear, and heavy impact.
HyppoCoat GC-H
HORIZONTAL WATERPROOFING SYSTEM
DETAILS
PROPERTIES | MEASUREMENT | TEST METHOD |
---|---|---|
Hardness (Shore A) | 50 ± 5 | ASTM D-2240 |
Tear Resistance | 40 ± 20 pli | ASTM D-624 |
Tensile Strength (psi) | 350 ± 50 psi | ASTM D-412 |
Elongation (%) | 300 ± 50% | ASTM D-412 |
Relative Density | 1.32 | - |
Solids - Weight (%) | 92 ± 3% | ASTM D-2369 |
Solids - Volume (%) | 90 ± 3% | ASTM D-2697 |
Viscosity (@ 80°F) | 5,000 ± 2,000 cps | - |
Service Temperature | -25°F to 200°F | - |
VOC | 0.83 lb/gal | ASTM D-2369-81 |
DETAILS
PROPERTIES | MEASUREMENT | TEST METHOD |
---|---|---|
Hardness (Shore A) | 45 ± 5 | ASTM D-2240 |
Tear Resistance | 35 ± 10 pli | ASTM D-624 |
Tensile Strength (psi) | 350 ± 50 psi | ASTM D-412 |
Elongation (%) | 300 ± 50% | ASTM D-412 |
Relative Density | 1.23 | - |
Solids - Weight (%) | 92 ± 3% | ASTM D-2369 |
Solids - Volume (%) | 90 ± 3% | ASTM D-2697 |
Viscosity (@ 80°F) | 40,000 ± 20,000 cps | - |
Service Temperature | -25°F to 200°F | - |
VOC | 0.83 lb/gal | ASTM D-2369-81 |