The Foreman’s Guide to Maintaining Black Pearl® Under Greenroof-Roofscapes®
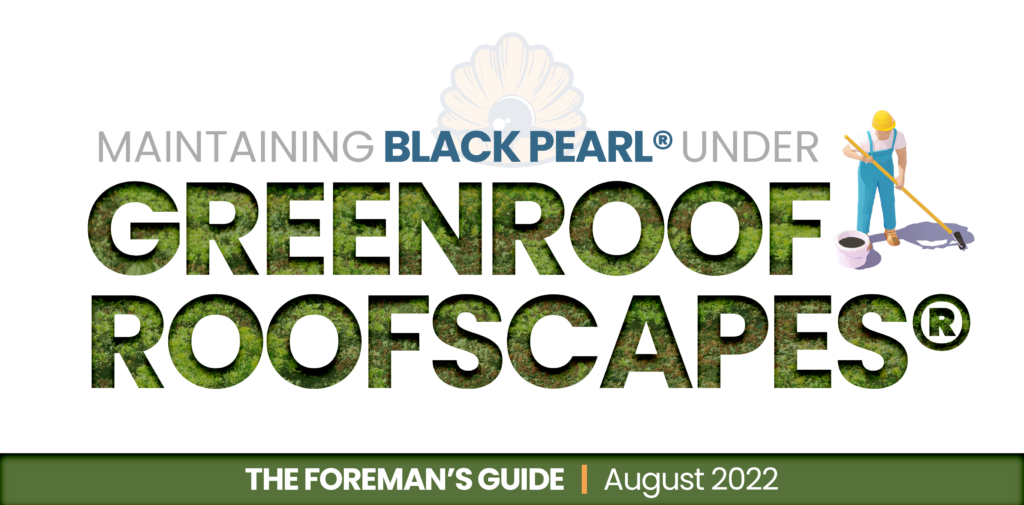
When it comes to implementing green roofs into building design, the benefits can be EXTENSIVE (pun intended).
But with any sort of ecosystem, sustainability and performance is dependent upon the level of protection & care it is given.
Performing routine, preventative maintenance is essential for keeping your green roof healthy & ensuring those benefits continue.
When a green roof is complete, most of the waterproofing membrane is covered with engineered soil & vegetation, limiting any inspection of the membrane to the elements that are visible or easily accessible. All green roofs must be inspected at least twice a year, generally in early spring & late fall, separate and apart from vegetation maintenance.
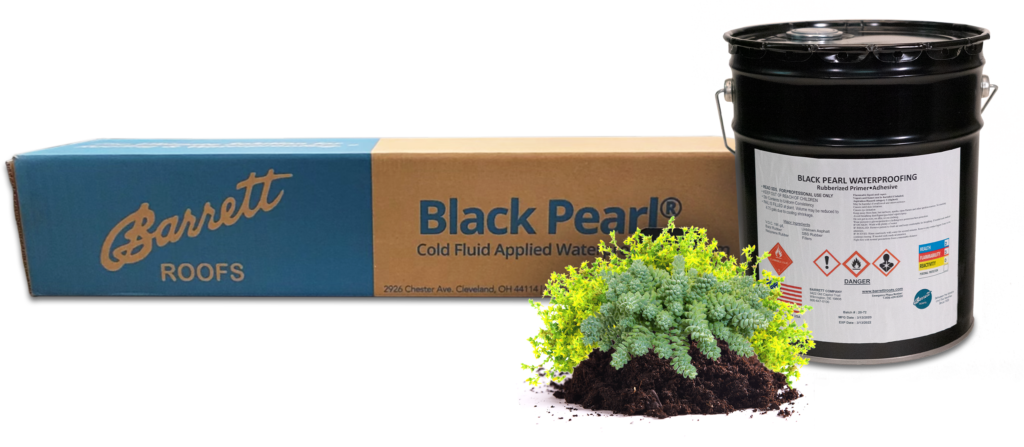
Black Pearl® Cold Applied Rubberized Asphalt Waterproofing System requires less maintenance than most other types of membranes. Semi-annual, scheduled inspections are not only prudent, they are cost-effective and can save considerable expense in preserving the warranty protection and extending the life of the system well beyond the warranty period.
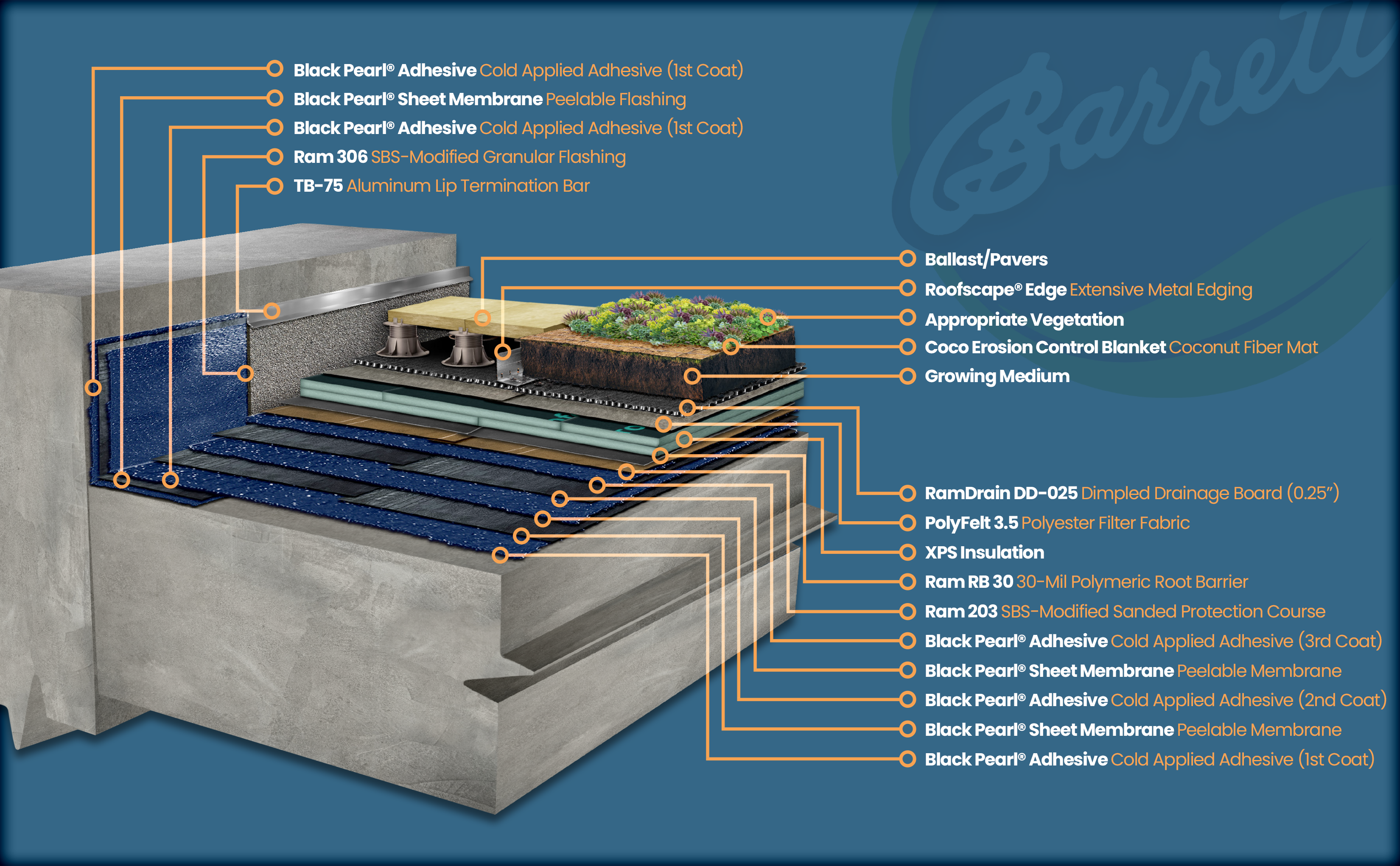
Green roof horticulture inspections will vary greatly from project to project depending upon the specific vegetation, depth of soil, weather conditions, irrigation, environmental conditions, and various other factors. Each project must be evaluated independently for the proper vegetation maintenance schedule. During the establishment period, a monthly inspection is generally sufficient for simple, basic, low-profile green roofs planted with sedum unless during drought periods. Drip irrigation systems will require less attention.
The following evaluation sequence is suggested for your maintenance personnel, professional maintenance services, or professional consultants for the membrane portion of the green roof.
PERIMETERS
Perimeters
Walk the perimeter of each deck and, to the extent possible, examine membrane base flashings, metal counter flashings, caulking sealants, termination bar and metal edging for mechanical damage. Even minor scrapes or punctures need to be properly repaired as soon as possible to prevent any progressive damage. Any loose metal must be re-attached properly, and all caulking must be maintained to prevent water entry around the flashing. If base flashings are bulging, check for water behind the flashing. Check masonry weeps. If water or masonry efflorescence (a whitish, chalky discoloration) is present on either side of the masonry, the source of the water entry must be determined and corrected as soon as possible.
DRAINS
Drains
Examine each drain and remove any debris that has collected around the drain. Ensure that drains are operative. On stone ballasted installations, keep larger stones around the drain strainer to help prevent clogging. Do not use any devices that will restrict water flow. Insure drain clamping ring is intact & tightly bolted to the sump.
ROOF SURFACES
Roof Surfaces
Roof surfaces should be always kept clean of debris. On stone ballasted surfaces, where the stone ballast has been displaced exposing the insulation or filter fabric, the stone and fabric must be put back into position. If stone ballast is consistently misplaced due to heavy traffic, such as near door openings or mechanical equipment, replace the stone ballast with concrete pavers.
This should also be done if building geometry and exposure results in localized stone “scrubbing” displacement from wind. Exposed filter fabric or insulation will deteriorate with direct exposure to ultraviolet rays. Inspect all concrete pavers and concrete wear slabs for signs of cracking, disintegration, or other types of breakage. If deterioration is occurring, determine the cause and institute corrective action as recommended by the manufacturer.
PENETRATIONS
Penetrations
Inspect all roof top penetrations such as vent pipes, exhaust fans, skylights, AC units, etc., checking for flashing tightness to substrate, metal flashings, seams, caulking sealants, termination bars, clamping rings and other visible elements.
If a new penetration must be installed through the deck, or if there is an addition to the existing building, contact the Barrett Company for recommendations. Barrett requires that any modifications to the membrane be performed by a Barrett Approved Contractor with Barrett materials of like and kind. This is an absolute requirement if the membrane is covered by a Barrett warranty.
REPAIR MATERIALS & CHEMICALS
Repair Materials & Chemicals
All petroleum-based products and harsh chemicals should be kept off the system. Any cleaning material, solvent, animal fats, grease, some water chiller chemicals, oil, or material containing any petroleum by-product, may degrade the membrane or other components. Any time such a product comes into contact with the membrane or insulation, an inspection is required to ascertain if damage has occurred.
If the membrane comes into contact with any type of chemical, contact Barrett Company for advice, since some chemicals can degrade the membrane, insulation or fabric. Black Pearl® or Ram Mastic is recommended for emergency repairs. Do not use random petroleum-based roof products to make repairs to the membrane. Contact Barrett for emergency repair recommendations.
Click Here to download your own digital copy of the “Maintaining Black Pearl® Under Greenroof-Roofscapes®” reference guide.
Looking to hire one of our various Approved Applicators for your next project? Interested in applying to become a Barrett Approved Applicator? Click Here to learn more!
NOTE: All product literature (i.e. technical & safety data sheets, specifications, application instructions, etc.) is currently available to download from the “Resource Library” on our website.
For questions regarding detailed specifications, application information, or any other general inquiries, please reach out to your local Barrett Technical Representative.
You can also call us directly at (800) 647-0100 or email us at info@barrettroofs.com