The Foreman’s Guide: The Two Most Important Principles of Waterproofing
THE MOST IMPORTANT PRINCIPLE OF WATERPROOFING
Each separate envelope trade contractor’s work, regardless of its being thought of as a waterproofing system or not (e.g., exterior mechanical apparatus), must become part of a totally watertight building envelope. Equally important, all individual envelope systems must be adequately transitioned into other components or provided with watertight terminations. Often the tradespeople completing this work are not aware of, trained in, or supervised in enveloping a building properly. And this is the number one cause of water infiltration in all types of structures.
The resulting improper attention to details is responsible for countless problems in construction. Properly detailing a building’s envelope presents an enormous task. From inception to installation, numerous obstacles occur. Highlighting this interrelationship of various envelope systems is the most important principle of waterproofing.
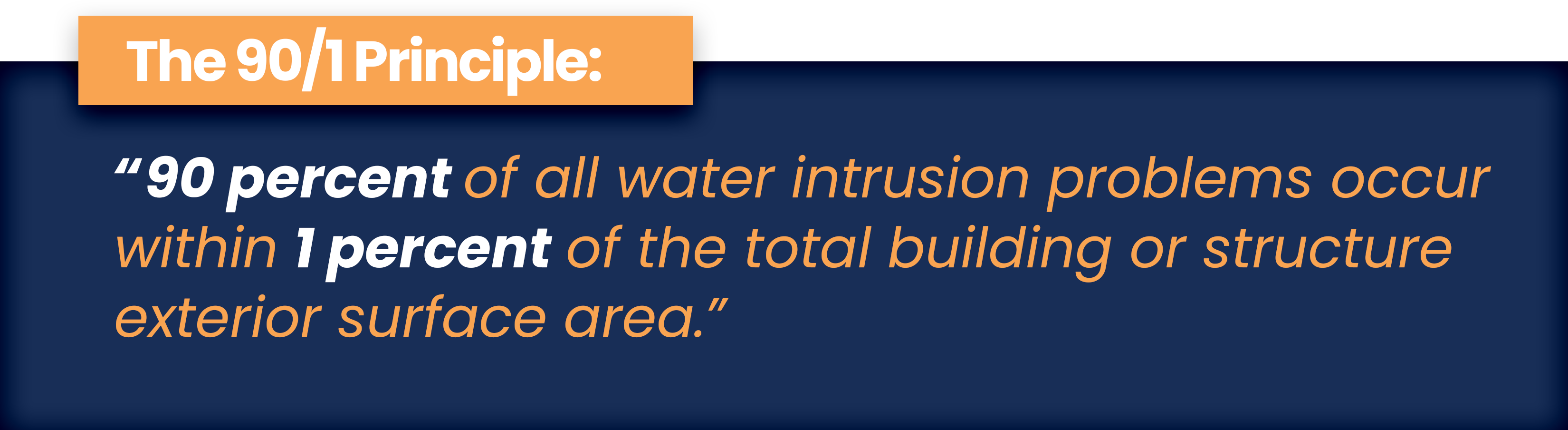
This 1 percent of a building’s exterior skin area contains the termination and transition detailing, as can be seen in the diagram below. This 1 percent area all too frequently leads to breaches and complete failure of the effectiveness of the building envelope and is the main cause of all waterproofing problems.
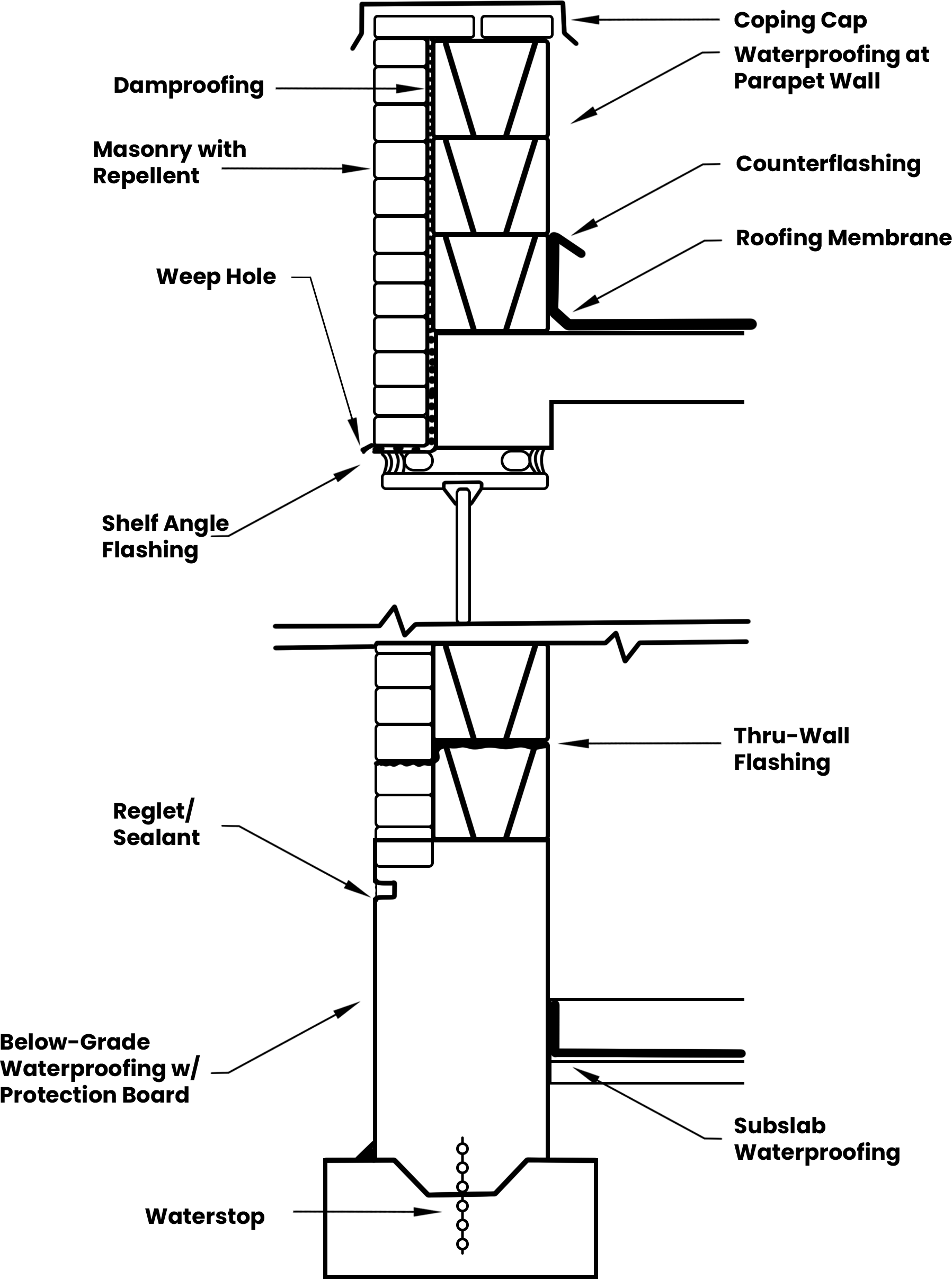
Industry members, including contractors, designers, and manufacturers, now are recognizing the importance of the 90%/1% principle; Architects must recognize the importance of these termination and transition detailing, manufacturers must provide the appropriate details with their specifications, and general contractors must provide the coordination and oversight of the numerous subcontractors involved in a single envelope for the completed product to perform as expected.
The 90%/1% principle is the reason that despite continuing technological advances, waterproofing continues to be one of the major causes of legal claims in the design and construction profession. It is not the actual manufactured waterproofing systems or envelope components that leak but the field construction details involving terminations and transitions.
THE SECOND MOST IMPORTANT PRINCIPLE OF WATERPROOFING
The inattention of detail is often exacerbated by overall poor workmanship that presents the next most important principle of waterproofing.
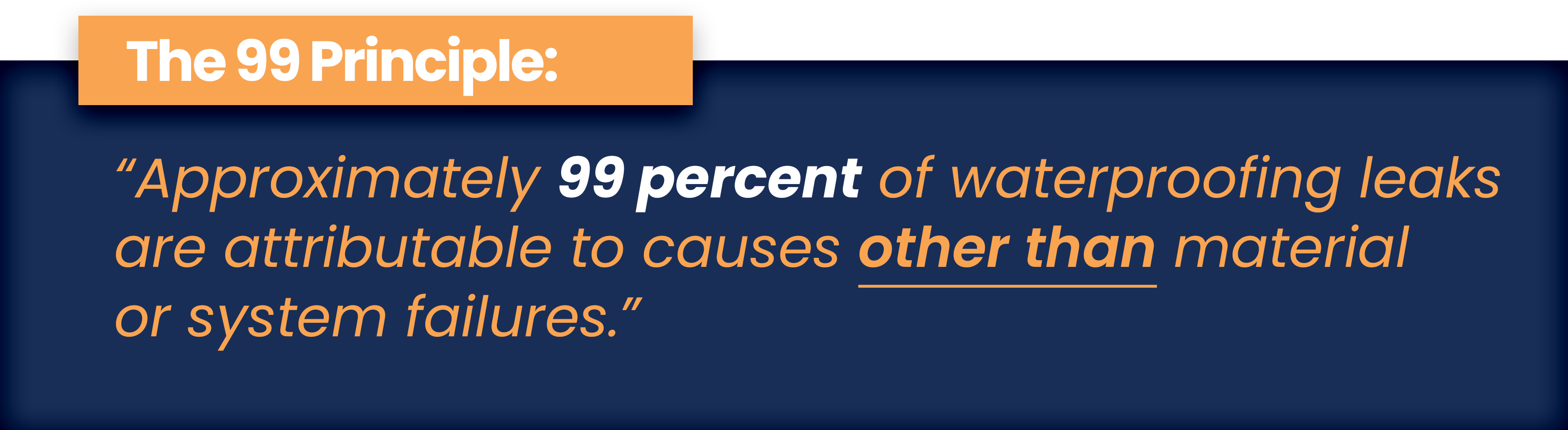
When considering the millions of square feet of waterproofing systems installed, both barrier and drainage systems, and miles of sealant involved in building envelopes, it can be estimated that only 1 percent of envelope failures and resulting leakage is actually attributable to materials or systems actually failing.
The reasons typically involved in failures include human installation errors, the wrong system being specified for in-place service requirements (e.g., thermal movement encountered exceeds the material’s capability), the wrong or no primer being used, inadequate preparatory work, incompatible materials being transitioned together, and insufficient—or in certain cases, such as with sealants, too much—material being applied.
Today, with quality controls and testing being instituted at the manufacturing stage, it is very infrequent that actual material failures occur. For example, it is rare to have an outright material failure for below-grade liquid applied membrane. More often than not, the leakage would be attributable to improper application, including insufficient mileage, improper substrate preparation, or applying over uncured concrete, among numerous other possible installation errors. Furthermore, it is likely that the leakage is also attributable to the 90%/1% principle, with inattention to proper detailing of terminations and transitions with the below-grade membrane occurring.
UNDERSTANDING THESE PRINCIPLES
These two important principles of waterproofing work in unison to represent the overall majority of problems encountered in the waterproofing industry:
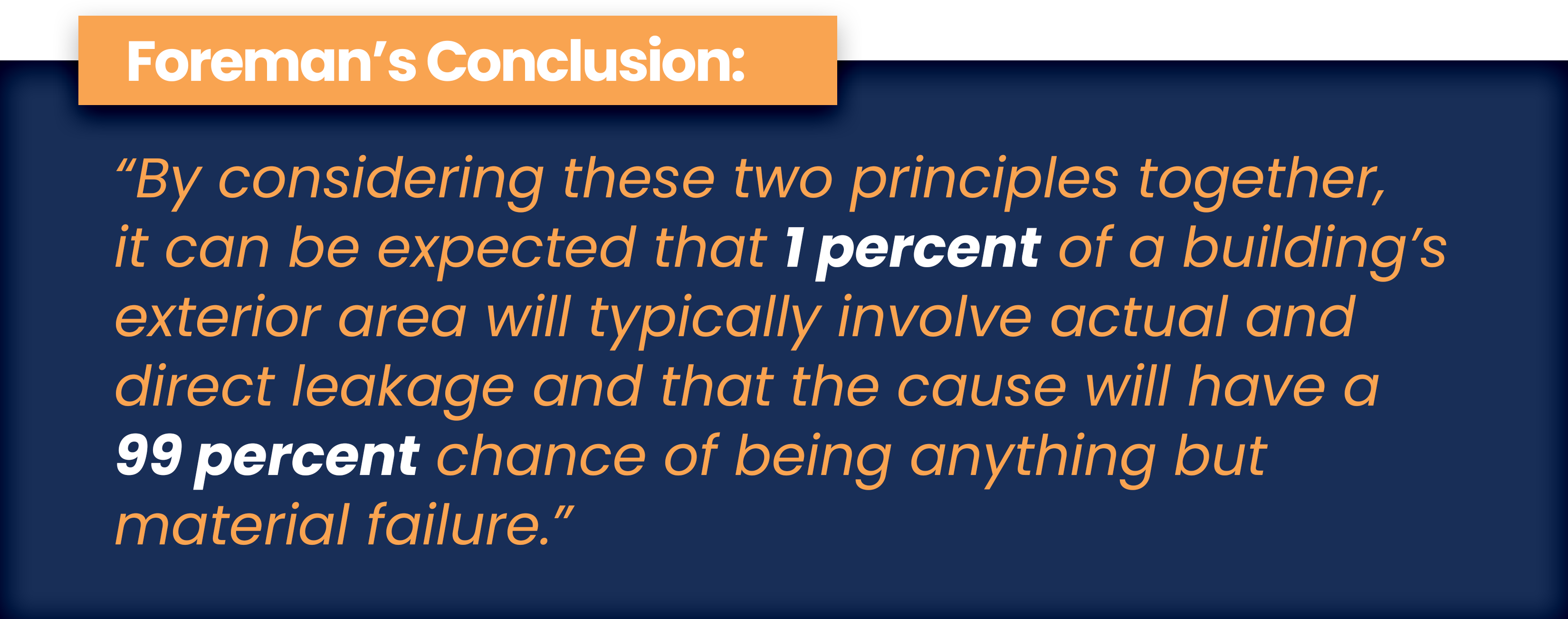
Considering that these two simple principles cover most leakage problems, it would seem that preventing water infiltration problems would be easy. Certainly, prevention of envelope failures must be a proactive process implemented before each actual field construction activities commence. One of the first steps to implement this quality control process is to encourage pre-construction envelope meetings that include all subcontractors involved in the building envelope and cover the following topics:
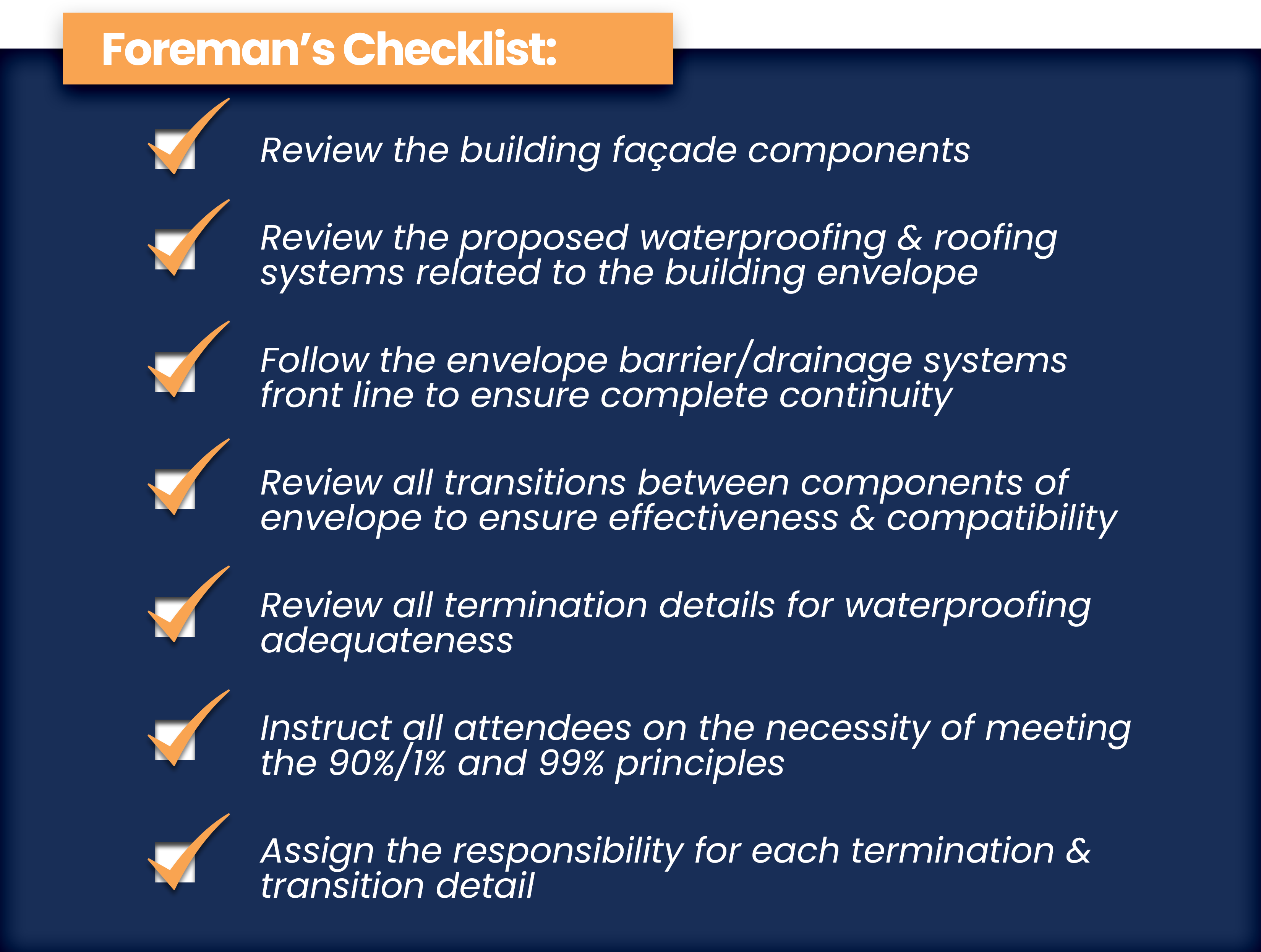
SERVICE WITH EXPERTISE
Service with expertise is the hallmark of every Barrett warranted project. Barrett’s understanding and acquired knowledge of roofing basics and material engineering concepts, from asphalt polymerization to felt condensing techniques; from workable flashing techniques to CAD detailing, is applied to each and every project by a Registered Roof Consultant or a corporate principle. To get the best performance from our roofing and waterproofing systems, the smart choice is to use a Barrett Approved Applicator.
Looking to hire one of our various Approved Applicators for your next project? Interested in applying to become a Barrett Approved Applicator? Click Here to learn more!
NOTE: All product literature (i.e. technical & safety data sheets, specifications, application instructions, etc.) is currently available to download from the “Resource Library” on our website.
**All data/information used in this blog courtesy of “Construction Waterproofing Handbook | Second Edition” by Michael T. Kubal
For questions regarding detailed specifications, application information, or any other general inquiries, please reach out to your local Barrett Technical Representative.
You can also call us directly at (800) 647-0100 or email us at info@barrettroofs.com