The Foreman’s Guide to Roof Coatings
When it comes to maintaining the roof of your home or commercial business, cold-applied coatings can be fundamental for performance and lifespan.
There are many reasons to apply a coating to your roof, though the most common is to maximize the service life by reflecting ultraviolet radiation away from the membrane. Coatings can be used with other roof repairs to restore an aged roof to a more maintainable waterproof condition, too. For many home and business owners, that is reason enough to invest in a roof coating treatment.
Understanding Roof Coatings
When determining which product is suitable for a specific project, always—and we mean, ALWAYS— examine the manufacturer’s material data sheets. Understanding the key differences between these materials can save a lot of time & money for the contractors, property owner, facility manager, and everyone else involved.
There are several types of coatings available on the commercial roofing market. However, the material formulations, uses, and application methods are all different.

Not all coatings are acceptable or compatible on all roof surfaces. Also, all pre-application preparation should be completed in accordance with the roof coating manufacturer’s requirements. As with all liquids and adhesives used in the roofing industry, proper on-site material storage is important, and all these products have a specified shelf life.
ELASTOMERIC ROOF COATINGS
Elastomeric coatings are generally a variety of products combined to form a strong compound, known as a hybrid. New formulations of these products are introduced to the market often. Some of the most common include neoprene, silicone, urethane, and latex/acrylic. These combinations are often compatible with the most common types of roofing material, though they tend to be most often used on metal or polyurethane foam roofing.
Acrylic
Acrylic elastomeric coatings are liquid-applied and dry to form a thick, fully adhered, monolithic (seamless) membrane in situ on the roof. Typically white in color, these coatings have the same viscosity as paint, which makes it brushable, rollable, or sprayable. Once dried, they are also fully adhered and entirely seamless.
Acrylic-based materials provide excellent resistance to radiation and hail damage and have the inherent flexibility required to withstand dimensional instability of most roof membrane surfaces. Some studies have indicated that properly formulated acrylic coatings can reduce surface temperature as much as 20°F when exposed to direct sunlight at 85°F. Acrylic coatings are economical, provide excellent reflectivity, and are easy to work with. These coatings also, however, lose mil-thickness from weathering, require application in ambient temperature of above 50 degrees F and, in certain cases, cannot withstand ponding water.
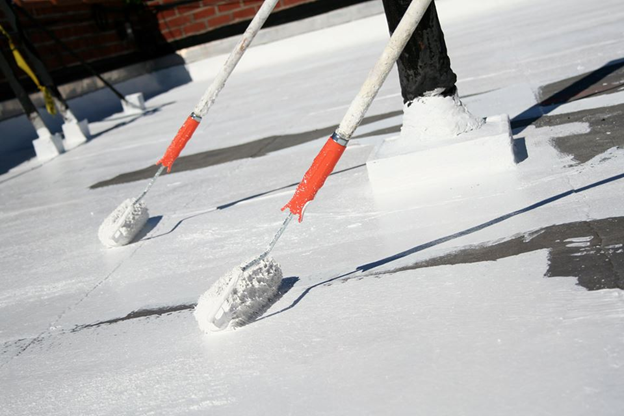
Barrett’s Solution:
Ram Ultra-White® Energy-Star® Rated Acrylic Elastomeric Roof Coating
Ram Ultra-White Coating is a co-polymer elastomeric water-based emulsion with a brilliant white color that offers excellent reflectivity, earning it an Energy Star® rating and LEEDS credits. It provides superior UV protection, mildew resistance, color stability, weatherability, and flexibility. Ram Ultra-White® not only helps provide protection from the elements, it provides substantial reduction of roof surface temperatures and thermal stresses, significantly increasing indoor comfort and saving cooling costs. Its ability to flex and move offers the elastic qualities necessary to accommodate the movement found in most polymer modified roof membrane systems.
PMMA (Polymethyl Methacrylate)
One of the most durable of all liquid membranes, these systems cure quickly and efficiently. With the use of catalysts, inhibitors, and separate grades (summer or winter), can be applied in a wide range of temperatures. Another advantage of PMMA liquid applied membranes is that their chemical bonds allow repairs to be easily made years later if needed. Some of the manufacturers have low VOC content so it can be used in enclosed areas (e.g., indoor fountains). These systems do have a limited “pot life”, so there a higher waste factor. Typical application is with squeegees and rollers which corresponds to higher labor costs.
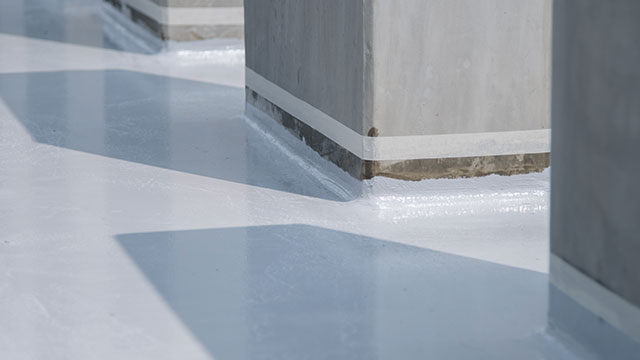
Barrett’s Solution:
Ram Quick Flash PMMA Polymethyl Methacrylate Roof Coating
The Ram Quick Flash PMMA roofing system is a fully reinforced, cold liquid-applied membrane system. It is based primarily upon Polymethylmethacrylate (PMMA) technology, incorporating a liquid component and a powdered catalyst, with each component curing in approximately one hour. A decorative PMMA finish can be applied as either a smooth color coating or a textured aggregate surfacing.the place of product installation.
Polyurethane
Polyurethane liquid membranes share many of the same advantages as PMMA products, including fast cure time and relative ease of patching. The main difference between PMMA and polyurethane-based systems are the number of components. There are multi-component polyurethanes and single-component polyurethanes. Multi-component polyurethanes have a faster cure time but a shorter pot life. Single-component polyurethanes have a longer cure time, but they do not have a pot life so there is less waste. Both systems can be applied with squeegee, roller, or sprayed with a special sprayer. Application via sprayer allows for a faster rate of installation, which in turn lowers labor cost. The disadvantage of Polyurethanes is that the system has temperature limitations for application (typically between 40-50 degrees and rising), so planning and scheduling of installation is key.
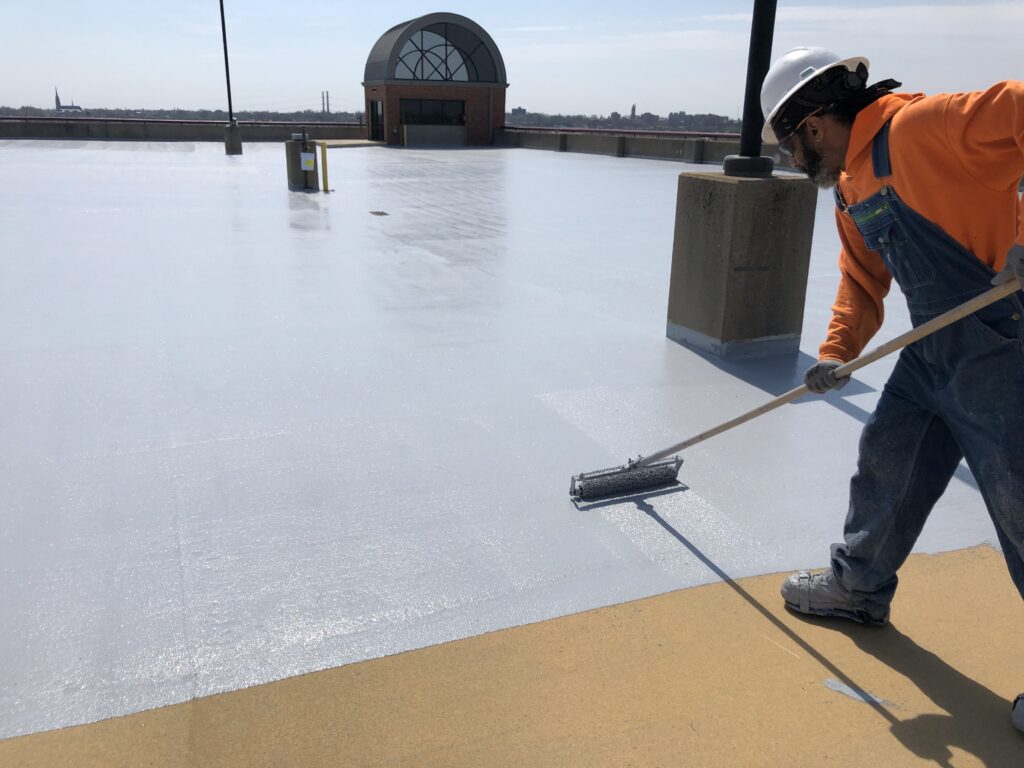
Barrett’s Solution:
HyppoCoat TC Two-Component Aliphatic Polyurethane Elastomeric Coating
HyppoCoat TC is a two-component, very high solids, aliphatic hybrid elastomeric topcoat. HyppoCoat TC is odor friendly, fast-setting, rapid-curing, and can be applied to properly prepared interior or exterior concrete, plywood and metal surfaces. It is suitable for single or multiple applications in temperatures as low as 20°F (-6.7ºC). Please use the correct product grade that complies with VOC regulations as per federal, state, county, and city regulations/codes that adhere to the location of product installation.
Silicone
Silicone-based liquid roof systems, in contrast to other liquid roof systems, can be applied without the use of a primer to the substrate in most instances. They are also applied via squeegee, roller, or sprayer. Silicone exhibits a high level of dimensional stability, and extreme temperature fluctuations. It has seen a rise in popularity in the commercial market over the last decade due primarily to the material’s ability to withstand long-term exposure to ponding water, which is an issue for most other coating options.
A silicone-based system has most of the same advantages as PMMA and Polyurethane systems but has a greater odor that could potentially limit its applications in sensitive areas/environments (e.g., hospitals and schools). Some of the drawbacks are cost, application requirements, and the fact that there are only a few materials – other than silicone – that can be applied directly to the silicone surface. Silicone also holds dirt on the surface and loses reflectivity over time.
ALUMINUM ROOF COATINGS
A silicone-based system has most of the same advantages as PMMA and Polyurethane systems but has a greater odor that could potentially limit its applications in sensitive areas/environments (e.g., hospitals and schools). Some of the drawbacks are cost, application requirements, and the fact that there are only a few materials – other than silicone – that can be applied directly to the silicone surface. Silicone also holds dirt on the surface and loses reflectivity over time.
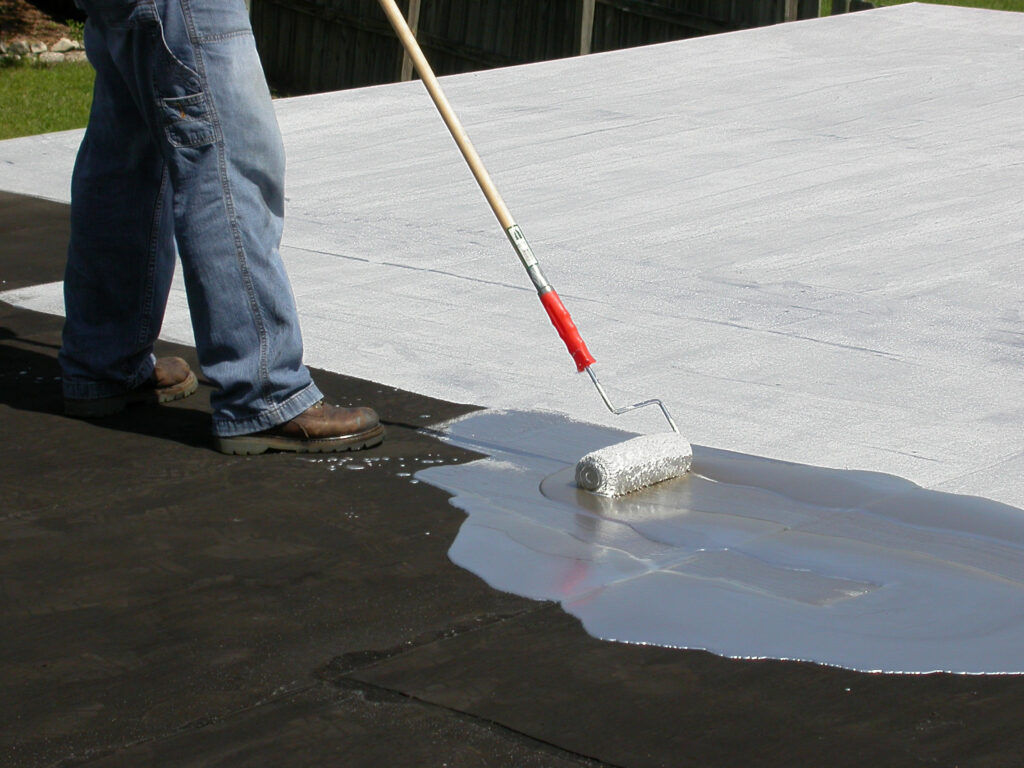
Barrett’s Solution:
Ram Ultra-Silver® Energy-Star® Rated Rubberized Aluminum Elastomeric Roof Coating
Ram Ultra-Silver is made of the highest quality SBS polymer-modified asphalt, premium aluminum pigment and refined solvents. When applied, aluminum flakes found in the pigment come to the surface providing a highly reflective metallic shield over the roof surfaces. This shield reduces surface temperatures and thermal movement. The SBS rubber provides elastic qualities necessary to accommodate the movement found in most polymer modified roof membrane systems. This combination of materials has proven itself as an excellent surfacing for both new and weathered asphalt built-up and modified bitumen roof systems. The reflective surfacing complies with current V.O.C. requirements and regulations. Consult the Barrett Company for specific installation recommendations for this product.
ASPHALTIC ROOFING MEMBRANES
If you’re looking for a strong, waterproof, and long-lasting architectural roofing system, an asphaltic, emulsion-based membrane system is a great option. Not only will it extend the longevity of your roof, but it can also easily be applied to a number of existing roof systems. Plus, they are compatible with most other roofing membranes and coatings.
These systems are economical in nature, making it affordable to build up a membrane of sufficient thickness to stabilize most existing roof substrates. It also saves materials by utilizing your failing roof system as a base and saving landfills from additional waste.
When speaking about roofing, the terms liquid membranes and liquid coatings are often used interchangeably. While there are some similarities between the two products, there are a few key distinctions. For a more complete breakdown of the distinction between the two, check out “The Foreman’s Guide to Roof Restoration.”
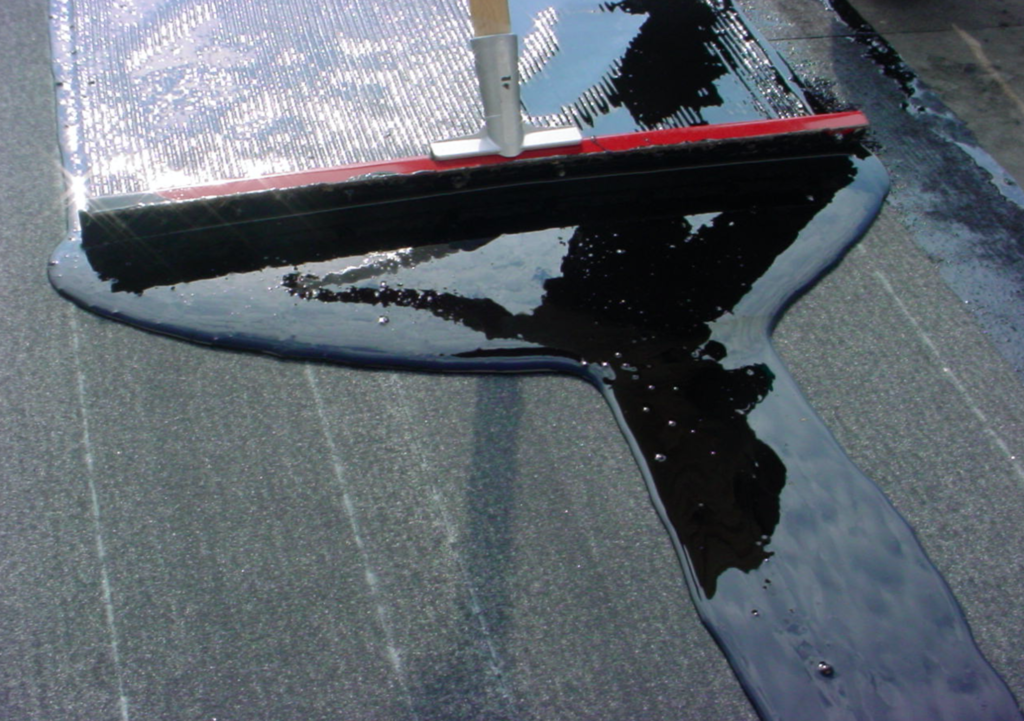
Barrett’s Solution:
Ram Cold Tar® Plus Energy-Star® Rated Rubberized Aluminum Elastomeric Roof Coating
Barrett’s Ram Cold Tar® Plus roofing-grade ply adhesive & waterproofing coating is a coal tar pitch-fortified, thermoplastic SEBS polymerized surfacing compound that is specially formulated to adhere to asphalt, modified bitumen, gravel surfaced, and coal tar roofing systems. Using the existing bituminous roof mat as a substrate, Barrett’s Ram Cold Tar® Plus fuses a new, high-strength, fluid-applied rubbery membrane to the mass of the old roof mat, creating a new, double thick, elastomeric waterproof membrane. The asphaltic rubber material combines the elastic properties of rubber with the waterproof/weatherproof characteristics of a highly refined emulsified asphalt. A surface coat of Ram Cold Tar® Plus not only offers a superior flexible weathering surface, but the resistance to ponding water, a well known characteristic of coal tar.
Looking to hire one of our various Approved Applicators for your next project? Interested in applying to become a Barrett Approved Applicator? Click Here to learn more!
NOTE: All product literature (i.e. technical & safety data sheets, specifications, application instructions, etc.) is currently available to download from the “Resource Library” on our website.
**All data/information used in this blog courtesy of “Construction Waterproofing Handbook | Second Edition” by Michael T. Kubal
For questions regarding detailed specifications, application information, or any other general inquiries, please reach out to your local Barrett Technical Representative.
You can also call us directly at (800) 647-0100 or email us at info@barrettroofs.com